Gedruckte Leiterplatten: dicke Zwischenlagen - Projektierung und Anwendung
Die Leiterplatten (PCBs) werden am häufigsten in elektronischen Niederspannungsgeräten und -Anlagen verwendet - es handelt sich um einen Bereich, in dem man stets bemüht ist, die Größe durch eine Reduzierung der Leiterbahnen zu minimieren. Die Leiterplatte wird auch zunehmend in Hochstromgeräten hoher Leistung mit einer erheblichen Stromdichte von leitfähigen Netzwerken eingesetzt. Leiterplatten dieser Art zeichnen sich durch eine große Kupferfolienstärke aus, die 105 µm und mehr erreicht.
In diesem Beitrag werden typische Anwendungen von Leiterplatten mit dicken Leiterbahnenlagen, Prinzipien der Projektierung von Leiterplatten, Vorteile und technologische Grenzen vorgestellt. Diese Informationen werden beim Entwerfen von Leiterplatten und bei der Optimierung ihrer kostenintensiven Herstellung hilfreich sein.
Leiterplatte - Anwendungen
Gedruckte Leiterplatten mit dicken Kupferfolienlagen können ein-, zwei- und mehrlagig hergestellt werden (das Aussehen solcher gedruckten Leiterplatten ist in Abb. 1 dargestellt). Derzeit werden solche Leiterplatten in vielen Industriebereichen eingesetzt: bei der Herstellung von Solarmodulen, Schweißgeräten, in verschiedenen Arten von Hochleistungsnetzteilen und -umrichtern, in der Automobil- und Bahnindustrie sowie im Energiebereich. Anfänglich wurden sie jedoch hauptsächlich in der Militär- und Luft- und Raumfahrtindustrie eingesetzt, wo sie vor allem in Geräten für Stromversorgungssysteme, Energiemanagement und -verteilung betrieben werden.

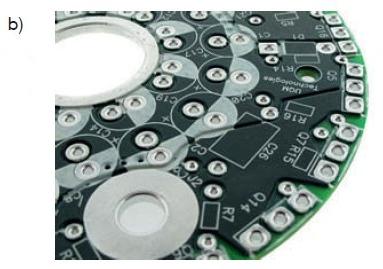
Vorteile der Verwendung von gedruckten Leiterplatten mit dicken Leiterbahnen
Gedruckte Leiterplatten mit dicken Leiterbahnenlagen haben eine Reihe von Vorteilen. Kupfer ist ein sehr guter Strom- und Wärmeleiter, daher verbessert die Verwendung von dicken Leiterbahnen die Wärmeübertragung quer durch und entlang des Umfangs, was wiederum schädliche Spannungen durch ungleichmäßige Erwärmung der Leiterplatte abbaut. Spannungen können zu Mikrorissen in Leiterbahnen führen, die zu periodischen oder dauerhaften Öffnungen und damit zum Geräteausfall führen.
Abb. 2. Wärmeübertragung und -ableitung durch Mosaike.
Der Vorteil einer dicken Leiterschicht ist auch der erhöhte Wärmewiderstand und die Strombelastbarkeit der Stromkreise, was die Zuverlässigkeit der Geräte verbessert, die unter ungünstigen Umgebungsbedingungen, insbesondere bei hohen Temperaturen, arbeiten. Auch die mechanische Beständigkeit von Kontaktstellen und metallisierten Löchern wird erhöht.
Eine effiziente Wärmeübertragung ermöglicht es, klassische Radiatoren direkt auf der Leiterbahnenfläche zu montieren. Es sind auch Lösungen üblich, bei denen sich die wärmeerzeugenden Leistungselemente auf einer Seite des Stromkreises befinden, während die gesamte andere Seite, mit einer Kupferschicht bedeckt, einen Radiator darstellt und der Wärmeübergang zwischen den Schichten durch Matrizen von Vias bereitgestellt wird (Abb. 2). Dank solcher Lösungen ist es möglich, die Produktions- und Montagekosten von Geräten bereits beim Entwerfen von Leiterplatten erheblich zu senken.
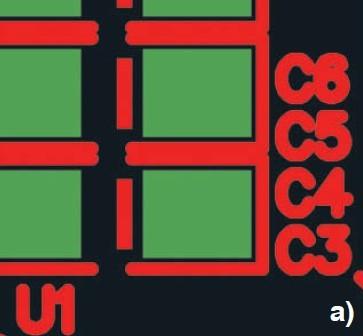
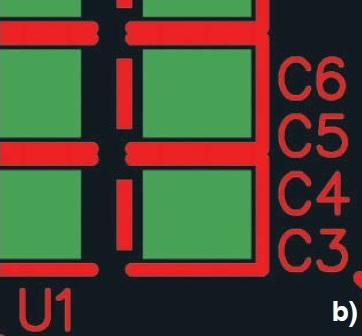
Entwerfen von Leiterplatten mit dicken Leiterschichten - die wichtigsten Regeln
Beim Design von Leiterplatten mit dicken Leiterschichten sollte man zuallererst die technologischen Möglichkeiten der Hersteller berücksichtigen, die wiederum von den zum Ätzen verwendeten chemischen Lösungen und den verfügbaren Maschinen bestimmt werden. Die technologischen Fähigkeiten des Herstellers werden durch die Werte der DRC-Parameter definiert (im Englischen: Design Rule Check) - sie bestimmen die minimal zulässigen Abstände zwischen den Elementen der Leiterbahnen und deren Abmessungen. Die DRC-Parameter des Leiterplattenherstellers TS PCB sind in der Tab. 1 zusammengefasst. Deutlich sichtbar ist die Zunahme der DRC-Parameter, die mit der Zunahme der Dicke der Kupferfolie einhergeht.
Tab. 1 zusammengefasst. Abhängigkeit der DRC-Parameter von der Anfangsdicke der Kupferfolie.
Parameter
|
Anfangsdicke der Kupferfolie
|
|||
105 µm
|
140 µm
|
175 µm
|
210 µm
|
|
Mindestabstand [mils]
|
13
|
15
|
20
|
27
|
Mindestbreite [mils]
|
12
|
14
|
18
|
25
|
Verlust [mils / mm]
|
Über 3 / 0,08
|
Über5 / 0,13
|
Über 6 / 0,15
|
Über 7 / 0,18
|
Beim Ätzprozess dicker Leiterbahnlagen tritt das Phänomen der sogenannten Unterwanderung - es äußert sich in einer Abnahme der Leiterbahnenbreite. Dies ist in der folgenden Abbildung dargestellt, die den Querschnitt des Laminats vor (Abb.3a) und nach dem Ätzen (Abb.3b) zeigt. Die Resist-Elemente sind eine Schutzschicht, deren Rolle für einseitige Leiterplatten ein Photopolymer spielt, während sich im Fall der zwei- und mehrlagigen Platten um das am Ende des Galvanisierungsprozesses aufgebrachte Zinn handelt. In Folge der Unterwanderung wird der Querschnitt der Bahnen reduziert und seine Form ändert sich von rechteckig zu trapezförmig.
Abb. 4. Laminatquerschnitt vor (a) und nach dem Ätzen (b).
Beim Entwerfen von Leiterplatten mit dicken Kupferfolienschichten ist der Füllungsgrad der inneren Lagen mit einem Leiter ein entscheidender Faktor. Eine zu geringe Kupferfüllung bei niedrigem Harzgehalt führt zum sogenannten "Harzhunger." Sie äußert sich in Hohlräumen zwischen den Schichten und führt zur Delamination des Materials. Auf diese Problematik wurde umfassender in einem vom Technologen der Fa. TS PCB, Herrn Rafał Tomaszewski, unter dem Titel „Aufbau, Eigenschaften und Entwerfen von mehrlagigen gedruckten Leiterplatten“ verfassten Beitrag eingegangen, der in der Juli-Ausgabe der Zeitschrift „Elektronik“ erschien.
Um das Phänomen der Delamination zu vermeiden, reicht es bei Innenlagen mit einer Kupferdicke von 105 µm und mehr aus, eine Kupferfüllung von mindestens 75 % bereitzustellen, während gleichzeitig eine möglichst gleichmäßige Kupferverteilung beibehalten wird. Bei der Auswahl der Art und Anzahl der Prepregs wird empfohlen, eine Software zur Unterstützung der Projektierung von Leiterplatten zu verwenden, z.B. MultiCal von Isola oder MultilayerArchitect von Technolam.
Nachstehend sind mit der Multical-Software erstellten Konstruktionszeichnungen dargestellt, die die Situation bei einer zu geringen (Abb. 4a) und einer richtigen (Abb. 4b) Kupferfüllung der leitfähigen Innenlagen betrachten. Im wirklichen Schaltkreis, der mit dem in Abb. 4a gezeigten Aufbau hergestellt wurde, tritt Delamination aufgrund von "Harzmangel" auf. Die Senkung der Kupferfüllung von 75 % auf 50 % reduziert den Harzfüllgrad um bis zu 69 %.
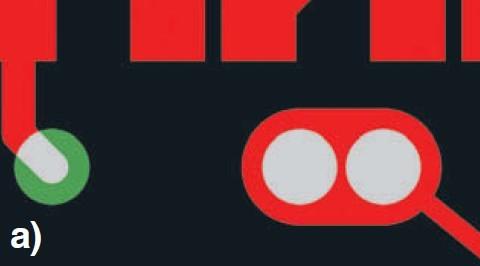
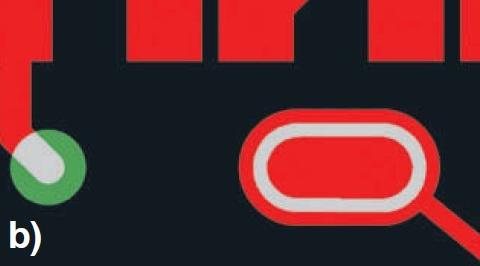
Zusammenfassung der wichtigsten Prinzipien zum Entwerfen gedruckter Leiterplatten mit dicken Schichten der Leiterbahnen
Dieser Text behandelt die Verwendungen und Eigenschaften von Leiterplatten mit dicken leitfähigen Schichten sowie die Regeln der Projektierung von Leiterplatten und technologische Einschränkungen. Die Verwendung der präsentierten Informationen macht möglich, auf das Erklären der Entwürfe in der Erstellungsphase der CAM-Fertigungsunterlagen zu verzichten und die Herstellkosten der Leiterplatten bei einer gleichzeitigen Aufrechterhaltung der Zuverlässigkeit und konstant hoher Qualität zu optimieren.