Aufbau, Eigenschaften und Projektierung von mehrlagigen gedruckten Leiterplatten
Von modernen elektronischen Geräten wird erwartet, dass sie hochfunktionell, kompakt und hochzuverlässig sind. Diese Merkmale werden dank einer großen Anzahl integrierter und miniaturisierter integrierter Schaltkreise erreicht, die durch komplexe Verbindungsnetzwerke verbunden sind. Das Abbilden von ihnen auf einer typischen zweiseitigen Leiterplatte nicht möglich, u.a. aufgrund der gewünschten begrenzten Größe des Schaltkreises. Daher ist es notwendig, mehrlagige Leiterplatten zu verwenden, manchmal mit High Density Interconnect (HDI)-Packungsdichte, typischerweise mit 4, 6, 8 oder mehr leitfähigen Lagen (Leiterbahnen). Der Beitrag enthält Informationen über den Aufbau, die Herstellung und die Techniken zur richtigen Projektierung von mehrlagigen Leiterplatten. Wenn diese befolgt werden, lassen sich Probleme bei der Projektierung des Stapels und der anschließenden Herstellung der Leiterplatten vermeiden.
Aufbau von Multilayer-Schaltkreisen
Im Gegensatz zu den zweiseitigen Leiterplatten ist der Aufbau der Mehrschichtlaminate viel komplexer und hat die Form eines Stapels (stack-up, build-up) mit einer geordneten Lagenstruktur, die normalerweise symmetrisch im Verhältnis zur Mitte ist. Im Querschnitt solcher Laminate gibt es drei Elemente: Kupferfolien sowie Kerne und Prepregs, die meist aus FR4-Laminat bestehen. Die gegenseitige Anordnung dieser Elemente ist durch die Norm IPC-2222 streng definiert, der zwei Arten des mehrlagigen Stapels vorsieht: Typ 1 und Typ 2. Diese beiden Arten der Lagenanordnung für einen beispielhaften 4-Schicht-Schaltkreis sind in Abb. 1 gezeigt.
Abb. 1. Lagenaufbau eines 4-lagigen Schaltkreises für Typ 3 (a) und Typ 4 (b)
Der als Typ 3 gekennzeichnete Schichtstapel ist sporadisch anzutreffen und wird für die Umsetzung von unkomplizierten Entwürfen verwendet. Bei dieser Variante ist die Ausführung von Vias, die die internen leitfähigen Schichten verbinden (vergrabene Vias) nicht möglich und die Herstellung von nicht durchgehenden Vias (blinde Vias) ist ein komplizierter technologischer Prozess. Der einzige Vorteil des Schichtstapels von Typ-3 ist seine etwas höhere Steifigkeit gegenüber dem Typ 4 bei gleicher Laminatstärke, insbesondere bei Designs mit sehr unterschiedlichen Kupferoberflächen der leitfähigen Schichten.
Abb. 2. Querschnitte von 4- (a), 6- (b) und 8-lagigen (c) Leiterplatten
Die gängigste Lagenanordnung bei Mehrschichtlaminaten, die für die Herstellung komplexer Projekte prädestiniert ist, stellt der Typ 4 dar. Sie wird von vielen Leiterplattenherstellern, darunter auch von der TS PCB, eingesetzt. Sie ermöglicht die Ausführung von auf den Kernen vergrabenen Vias und das relativ einfache Bohren von blinden Vias. Darüber hinaus bietet Typ 4 aufgrund der Möglichkeit, Prepregs unterschiedlicher Dicke miteinander zu verbinden, eine große Flexibilität bei der Gestaltung der Stärke sowohl der Prepreg-Lagen als auch des kompletten Laminats. Aus diesen Gründen konzentriert sich der nachstehende Beitragstext auf mehrlagige Leiterplatten Typ 4.
Beispiele für 4-, 6- und 8-lagige Schaltkreisstapel sind in Abb. 2 dargestellt. Die Abbildung zeigt, dass das Innere des Schichtstapels Kerne beinhaltet, die aus einem beidseitig mit Kupferfolie beschichteten Dielektrikum mit Struktur eines zweiseitigen Laminats bestehen und leitfähige Innenschichten der mehrlagigen Leiterplatten bilden. Die äußeren Lagen des Schichtstapels bestehen aus Kupferfolien mit abgebildeten Leiterbahnen der oberen und unteren Lage. Kupferkerne und -folien sind durch Prepregs getrennt, deren Aufgabe es ist, den Stapel unter Einhaltung entsprechender Abstände fest und dauerhaft zusammenzukleben.
Materialien für mehrlagige Leiterplatten
Parameter der Komponenten mehrlagiger Stapel und insbesondere deren Stärken sind genormt. Nachfolgend werden die Katalogdaten der am häufigsten verwendeten Kupfer-Prepregs, -Kerne und -Folien dargelegt.
Prepregs werden als einzelne Glasfasern hergestellt, die mit unvollständig polymerisiertem Epoxidharz angereichert sind. Beim Pressvorgang schmelzen sie durch hohe Temperatur und hohen Druck und verkleben miteinander die einzelnen Lagen des Stapels. Auf dem Markt sind zahlreiche Arten von Prepregs mit unterschiedlichen Stärken und Harzgehalten vorhanden.
Tab. 1. Parameter der am häufigsten verwendeten Prepregs
Die meisten Leiterplattenhersteller bieten jedoch 3-4 Typen an (Tab. 1), die entsprechende Qualitätsparameter der Leiterplatten und eine optimale Flexibilität beim Aufbauen der Stapel gewährleisten. Im Hintergrund eines solchen Vorgehens stehen hauptsächlich wirtschaftliche Erwägungen. Prepregs zeichnen sich durch eine relativ kurze Haltbarkeit aus, daher würde die Lagerhaltung von mehreren Prepregs den Leiterplattenhersteller der Gefahr von großen Verlusten aussetzen, da viele Typen, insbesondere solche mit schwacher Drehung des Lagerbestands, unterhalten werden müssten
Tab. 2. Parameter gängiger Kerne
Wie bereits erwähnt, handelt es sich bei den Kernen um zweiseitig kupferplattierte Laminate typischer Stärken: 18, 35 (Standard), 70 und 105 µm. Wie bei Prepregs sind die Kernstärken unter Berücksichtigung der Stärke der Kupferfolie genormt und bilden eine Typenreihe. Die verfügbaren typischen Kernstärken und die zu deren Herstellung verwendeten Prepregs sind in der Tabelle 2 zusammengefasst.
Leiterplattenhersteller verfügen wie bei Prepregs über eine Dutzend der gängigsten Kerne, auch mit unterschiedlichen Kupferfolienstärken und in Ausführungen mit erhöhtem Tg-Parameter (150 und 180oC). Die Typenreihe der Kupferfoliestärken ist analog zu den Kernen, d.h.: 18, 35, 70 und 105 µm. Sie ermöglichen nach dem Metallisierungsprozess das Erreichen von den folgenden Stärken der Kupferschicht: 35 (Standard), 70, 105 und 140 µm.
Prinzipien beim Konstruieren der Leiterplatten
Der Designprozess eines mehrlagigen Stapels besteht darin, solche Parameter der Komponenten zu kombinieren, die die vorausgesetzten elektrischen Eigenschaften (Ströme, Impedanzen, Widerstandsfähigkeit gegen Durchschlag) und mechanischen Eigenschaften (Stärke, Steifigkeit, einfache Verarbeitung) des Laminats sicherstellen. Es gilt, Parameter auszuwählen im Hinblick auf:
- Kerne, um die gewünschte Anzahl der Lagen zu erhalten, den Abstand zwischen den äußeren Schichten der einzelnen Kerne und die Stärke der leitfähigen Innenschichten,
- Prepregs, die ausreichende Abstände zwischen den Kernen untereinander sowie zwischen den Kernen und den äußeren Lagen der Leiterbahnen bei einer ausreichenden Harzfüllung gewährleisten,
- Kupferfolien unter Berücksichtigung der DRC-Parameter der äußeren Leiterbahnen der Platine.
Der Aufbau eines mehrlagigen Stapels sollte bereits in der Entwurfsphase die technologischen Möglichkeiten und Materialien berücksichtigen, die dem Leiterplattenhersteller zur Verfügung stehen. Die Verwendung ausgesuchter Kerne und Prepregs und deren untypische gegenseitige Anordnung kann im Extremfall die Herstellung der Leiterplatte unmöglich machen.
Normalerweise schlägt der Hersteller in solchen Situationen alternative Aufbauoptionen mit Parametern vor, die dem Original so nahe wie möglich kommen, aber sich auf verfügbare Materialien stützen. Das Erzwingen der Ausführung eines Stapels von nicht standardmäßigen Materialien wird sicherlich den Zeit- und Kostenaufwand für die Projektdurchführung erhöhen, da diese bestellt werden müssen, es sei denn, es liegen andere technologischen Voraussetzungen vor, die die Möglichkeit der Herstellung ausschließen.
Es wird empfohlen, nach Möglichkeit symmetrische Stapel in Bezug auf die Querschnittsmitte zu verwenden, um ähnliche Oberflächenspannungen auf den beiden Laminatseiten zu erhalten. Dieser Vorschlag gilt auch für die Verteilung der Kupferoberfläche auf Leiterbahnen, insbesondere der Innenschichten. Manchmal lässt sich ein symmetrischer Aufbau nicht erreichen, beispielsweise auf Grund bestimmter Impedanzen der Übertragungsleitungen, was zur Verwindung der fertigen Schaltungen bei der Montage (Löten) führen kann.
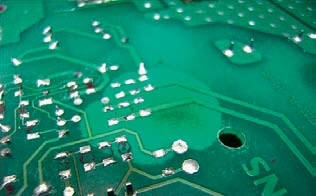
Abb. 3. Beispiel für Delamination
Beim Aufbau eines Stapels sollte die Regel befolgt werden, dass benachbarte leitfähige Lagen durch mindestens zwei Prepregs getrennt sind. Die Verwendung eines einzelnen Prepregs kann zur Bildung von Leckströmen und Delaminationsstellen führen, da die Glasfasern beim Pressen insbesondere an den Rändern der Platine beschädigt werden können.
Die Anzahl und Art der verwendeten Prepregs ist im Hinblick auf das Füllen der Bereiche zwischen den leitfähigen Schichten mit Harz entscheidend und hängt von der Stärke der leitfähigen Lagen und deren Kupferfüllung ab. Eine unzureichende Harzfüllung verursacht das eines „Harzhunger“-Phänomen (resin hunger), der zur Bildung von Hohlräumen zwischen den Lagen und anschließend zur Abspaltung von Lagen und deren Delamination führt (Abb. 3). Sie können auch zur Bildung von Korrosionspots und Leckströmen führen, da die Produkte des Galvanisierungsprozesses in ihnen eingefangen werden.
Die benötigte Harzmenge lässt sich am besten mithilfe spezieller Programme nachprüfen, die für Projektierung und Kontrolle der mehrlagigen Stapeln gedacht sind und auf den Websites namhafter Laminathersteller kostenlos zur Verfügung stehen. Die gängigsten Programme sind Multical (Isola) und Multilayer Architect (Technolam).
Ein Vergleich der im Multical-Programm entwickelten Stapel mit korrekter (Abb. 4a) und unzureichender Harzfüllung (Abb. 4b) ist im nebenstehenden Bild dargestellt. Das Problem des Harzmangels kann auf verschiedene Weise gelöst werden: Vergrößern der Kupferfläche auf den Innenlagen, Verwenden eines Prepregs mit höherem Harzgehalt (mit MR- oder HR-Kennzeichnung) oder Verwenden eines zusätzlichen Prepregs, was leider die Erhöhung der Stärke des Dielektrikums und damit des gesamten Laminats verursacht.
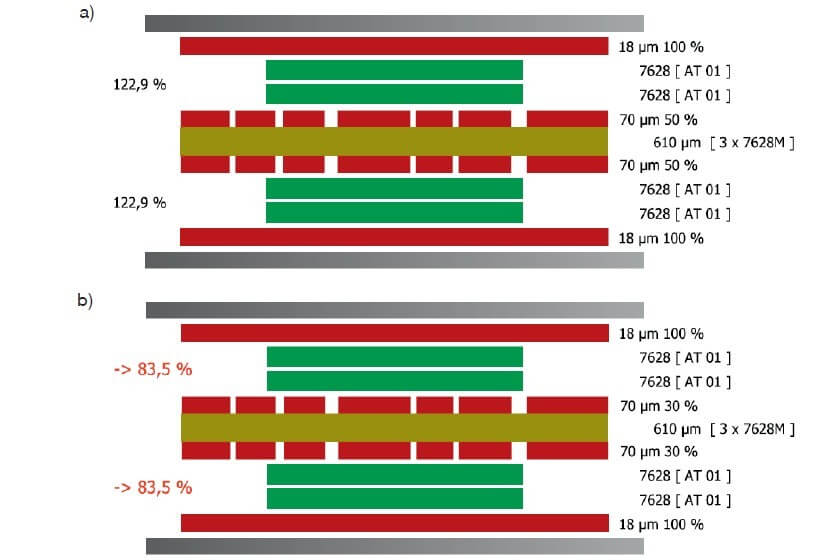
Abb. 4. Aufbau mit richtigem (a) und zu niedrigem (b) Harzgehalt im Multical-Programm
Ein weiterer Vorteil dieser Art von Programmen besteht in der Möglichkeit, den Abstand zwischen den Lagen und die endgültige Laminatstärke nach dem Pressen im Vergleich zu herkömmlichen mathematischen Berechnungen genau zu bestimmen. Die Abb. 5 zeigt einen Vergleich des Abstands zwischen den Lagen, der anhand einer Kalkulation, der Ermittlung im Multical-Programm und eines mikroskopischen Schliffbilds (Querschliff, Mikrobild) für einen beispielhaften Stapel einer vierlagigen Schaltung ermittelt wurde.
Abb. 5. Vergleich der Dicken der berechneten Schichten (a), ermittelt in der Multical-Software (b) und der gemessenen in der tatsächlichen 4-Schicht-Schaltung (c)
Für diese Schaltung ging der Konstrukteur davon aus, dass die Abstände zwischen den Lagen 180 µm betragen müssen. Zu diesem Zweck wurden anhand der Tab. 1 zwei Prepregs 2125 verwendet. Bei der Projektierung mit dem Multical-Programm, das die Kupferflächenwerte auf den Innenlagen und den Harzgehalt in den Prepregs berücksichtigt, zeigt sich jedoch, dass die Gesamtstärke der beiden Prepregs 2125 um ca. 10 µm größer ist.
Die Ergebnisse des genommenen Schliffbilds der tatsächlichen Schaltung bestätigten, dass die Stärke des Dielektrikums ca. 190 µm beträgt, was dem Ergebnis aus dem Multical-Programm nahekommt. Eine vollständige Übereinstimmung der Stärke der Prepreg-Lagen und -Kerne mit den in Multical ermittelten Werten ist aufgrund der Stärkentoleranz dieser Materialien unwahrscheinlich.
Einige Projekte elektronischer Anlagen, beispielsweise solche, die mit hohen Spannungen zusammenhängen, erfordern die Verwendung von Kernen mit einer Stärke von mehr als 1 mm. Diese Arten von Kernen sind meistens bei Leiterplattenherstellern auf Grund der niedrigen Marktgängigkeit nicht erhältlich. Es ist jedoch möglich, sie indirekt durch Pressen zweier dünnerer Kerne, durch Prepregs getrennt, zu erhalten. Der Kern entspricht in diesem Fall dem Stapelaufbau vom Typ 3, jedoch mit einer innenliegenden geätzten Kupferschicht. Ein Beispiel für einen Stapel der Leiterplatte mit einem 1,6 mm starken Kern ist in Abb. 6 dargestellt.
Zur Erhöhung der Packungsdichte von Elementen werden bei mehrlagigen Leiterplatten für die angenommene Anzahl der Lagen vergrabene und blinde Vias verwendet. Wie bereits erwähnt, ermöglichen die vergrabenen Vias die Verbindung von Leiterbahnen innerhalb einzelner Kerne und benötigen keine Oberfläche auf den äußeren Schichten, die beispielsweise für die Montage von Elementen genutzt werden kann. Es sei daran erinnert, dass der maximale Durchmesser von vergrabenen Vias aufgrund möglicher Entstehung von Delaminationsstellen begrenzt ist. Der Hersteller TS PCB empfiehlt die Verwendung von vergrabenen Vias mit einem Durchmesser von nicht mehr als 1,5 mm.
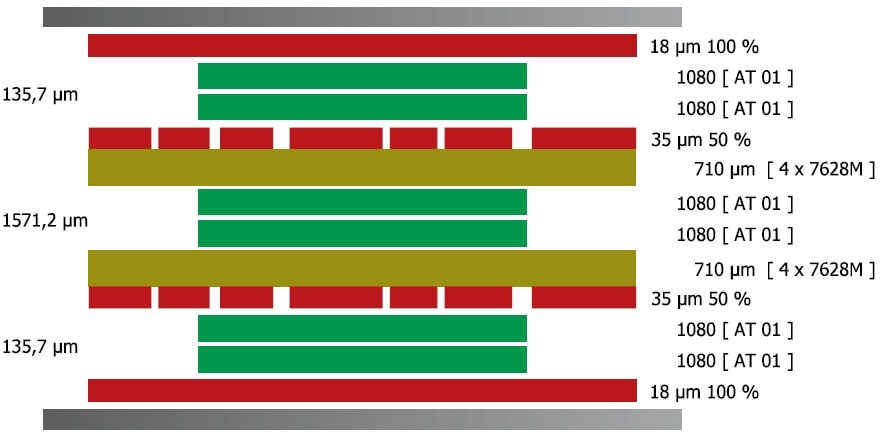
Abb. 6. Beispiel für einen Stapel mit 1,6 mm Kern
Blinde Vias ermöglichen es Ihnen, eine der äußeren leitfähigen Lagen mit einer oder mehreren inneren Lagen zu verbinden. Dadurch entsteht auf der gegenüberliegenden äußeren Schicht ein Freiraum im Vergleich zu einem herkömmlichen Via, der beispielsweise zum Routing von Verbindungsnetzwerken genutzt werden kann.
Eine gewisse Einschränkung für blinde Vias besteht in der Abhängigkeit ihres Durchmessers von der zulässigen Bohrtiefe und damit der möglichen Anzahl zu verbindender Lagen. Der kleinstmögliche Abstand zwischen den zu verbindenden Lagen trägt zur Verringerung der blinden Vias bei. Wenn nichts anderes dagegen spricht, wird empfohlen, diese auf möglichst dünnen Laminaten mit einer Stärke von weniger als 1 mm zu verwenden.
Wenn eine größere Materialstärke erforderlich ist, lohnt es sich, den Schaltkreis so zu gestalten, dass die blinden Vias nur die äußeren Lagen mit den nächstgelegenen inneren Lagen verbinden, diese Lagen mit zwei 1080-Prepregs zu trennen und die erwartete endgültige Laminatstärke durch Verwendung von dickeren Kernen zu erreichen.
Zusammenfassung
Der Beitrag beschreibt den Aufbau mehrlagiger Stapel, Parameter der verwendeten Materialien und Prinzipien der richtigen Konstruktion von Leiterplatten. Es wurden Werkzeuge vorgestellt, die den Projektierungsprozess der Stapel erleichtern und sicherstellen, dass die gewünschte endgültige Stärke sowohl der Prepreg-Schichten als auch des kompletten Laminats korrekt mit Harz gefüllt wird. Die Einhaltung der oben genannten Grundsätze macht es möglich, zahlreiche Probleme im Zusammenhang mit der Herstellung und Montage dieser Art von Leiterplatten und die damit verbundenen zusätzlichen Kosten zu vermeiden.