Jak poprawnie projektować panele dla obwodów o niewielkich rozmiarach? - część 1
Kierunek rozwoju branży producentów elektroniki wyznacza stale postępujący trend miniaturyzacji sprzętu elektronicznego, przy jednoczesnym wzroście jego funkcjonalności. Tendencja związana z miniaturyzacją samych urządzeń jest już powszechnienie znana, wiąże się ona także z redukcją fizycznych rozmiarów samych obwodów drukowanych, co ma bezpośredni wpływ na proces ich produkcji i montażu.
Obwody o rozmiarach 50 mm i mniejszych powinny być produkowane w panelach. Ich projektowanie zaś sprowadza się do podjęcia dwóch decyzji: o optymalnym rozkładzie i ilości obwodów oraz o wyborze odpowiedniej obróbki mechanicznej, biorąc pod uwagę zarówno rozmiar, kształt pojedynczych płytek jak i grubość laminatu. Projektanci nie zauważają często bardzo istotnej kwestii jaką jest zachowanie właściwego rozkładu miedzi na obwodach i na ramce panelu. Poprawnie zaprojektowany panel zapewni optymalny montaż elementów oraz łatwą separację zmontowanych obwodów przy możliwie najmniej skomplikowanym procesie produkcji. Zagwarantuje także integralność obwodów w procesie produkcji oraz podczas transportu paneli do montażysty.
Zasady poprawnego układania paneli dla małych obwodów, bazujące na doświadczeniu inżynierów CAM firmy TS PCB Techno-Service, zostaną opisane w dalszej części artykułu. Wiedza z tego zakresu może przynieść korzyści w zakresie:
- poprawy mechanicznej stabilności panelu,
- optymalizacji procesu montażu,
- separacji obwodów,
- obniżenia kosztów wytworzenia płytek.
Obwody o niedużych wymiarach
Jedynym z istotnych ograniczeń w produkcji niewielkich i pojedynczych obwodów drukowanych jest obróbka mechaniczna. Pozwala ona na swobodne wyodrębnienie płytek z formatu produkcyjnego. Minimalna wielkość pojedynczego obwodu w TS PCB Techno-Service S.A. powinna posiadać rozmiar 30 x 30 mm. Wymiar ten wynika ze specyfiki procesu obróbki mechanicznej.
Podczas frezowania (fot. 1) za narzędziem podąża dysza wyciągu mającego usuwać resztki frezowanego laminatu. W przypadku niewielkiej, lekkiej płytki podciśnienie może zaciągnąć ją jako odpad lub, co gorsze, przesuwać już wycięte płytki po laminacie, powodując rysowanie powierzchni pozostałych obwodów. W przypadku rylcowania pojedynczych płytek o wymiarach mniejszych niż 30 mm problematyczne staje się ich wyłamywanie z formatu. Proces separacji jest wówczas niezmiernie czasochłonny oraz kosztowny. W przypadku obwodów, których jeden z rozmiarów jest mniejszy 5 mm, wyłamanie bez ryzyka uszkodzenia obwodu jest praktycznie niemożliwe.
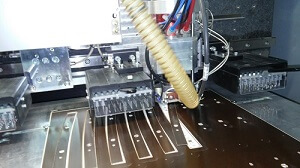
fot.1 Frezowanie końcowe płytek.
Panel rylcowany
Najlepszym rozwiązaniem dla małych obwodów jest zastosowanie panelu rylcowanego, zapewni on jego stabilność oraz późniejszą łatwość separacji.
Rylcowanie polega na obustronnym nacinaniu laminatu tarczowymi ostrzami. Powstałe rowki umiejscowione są na krawędziach płytek w panelu (fot. 2).
Standardowa grubość nierylcowana, czyli taka która umożliwia utrzymanie obwodów w panelu, wynosi 0,3÷0,5 mm. Panel rylcowany zapewnia wysoką sztywność, bez względu na ilość płytek. Nie wymaga on również zastosowania dodatkowych marginesów lub ramek, o ile nie jest to konieczne z innych względów (np. do montażu).
Bezsporną zaletą paneli rylcowanych jest maksymalne wykorzystanie materiału. Nie jest także konieczne stosowanie dodatkowych odstępów pomiędzy płytkami, które ostatecznie i tak staną się odpadem. Nie oznacza to jednak, że nie istnieją ograniczenia w stosowaniu tego typu paneli. Podstawowym warunkiem wykluczającym rylcowanie jest grubość laminatu, musi wynosić ona co najmniej 0,5 mm. Podobnie jakość wykończenia krawędzi obwodów oraz tolerancja ich wymiarów jest dużo mniejsza niż dla obróbki frezowaniem. Tarcze nacinające rowki pracują jedynie w dwóch kierunkach: pionowym i poziomym. Z tego powodu przygotowanie paneli o rylcowanych krawędziach jest możliwe wyłącznie dla obwodów prostokątnych.
Rylcowanie wymaga także zastosowania konkretnych zasad przygotowania mozaik, ponieważ rowki wyznaczające krawędzie obwodów posiadają określoną szerokość. Projektując obwód należy zachować odpowiednią odległość elementów mozaik od krawędzi, tak aby nie zostały one uszkodzone podczas procesu. Szerokość rowków a w ich następstwie, minimalny dystans mozaik od krawędzi, zależą od grubości laminatu. Dla standardowego laminatu 1,55 mm odległość ta wynosi aż 0,4 mm (rys. 3), podczas gdy dla krawędzi frezowanej jest to jedynie 0,15 mm.
Panele rylcowane nie mogą być stosowane w grubszych laminatach, o ile montażysta nie posiada specjalnego separatora paneli lub gilotyny. Grubość nierylcowana dla laminatów powyżej 2,4 mm, musi wynosić więcej niż standardowe 0,5 mm. Panel może bowiem rozpaść się w trakcie produkcji pod wpływem własnego ciężaru. Uniemożliwia to ręczną separację panelu bez ryzyka uszkodzenia obwodów. Z tego powodu właśnie panele na grubym laminacie wykonuje się jako frezowane.
Panele w całości rylcowane należy stosować dla pojedynczych obwodów o rozmiarze nie mniejszym niż 30 mm, ponieważ separacja mniejszych obwodów bez dodatkowych specjalnych narzędzi jest w zasadzie niemożliwa. Tego typu obwody powinny być produkowane w panelach w całości frezowanych lub o mieszanej obróbce z uwagi na łatwiejszą późniejszą separację.
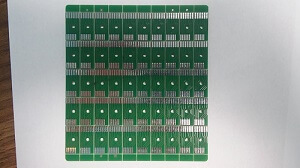
fot.2 Panel rylcowany z marginesami (góra i dół).
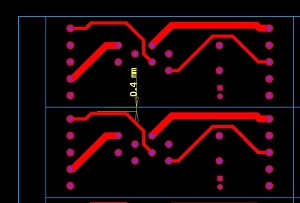
rys.3 Odległość ścieżki od krawędzi rylcowanej.
Panel frezowany
Panele frezowane stosuje się w przypadku kiedy nie jest możliwe wykorzystanie rylcowania.
Posiadają one mostki łączące płytki pomiędzy sobą lub / i z ramką panelu. Ten typ panelu jest dedykowany dla obwodów o rozmiarach poniżej 30 mm niezależnie od kształtu, lub większych o nieregularnym kształcie (np. koła, elipsy).
Konstruowanie panelu frezowanego wymaga zastosowania kilku zasad. Najlepiej budować go z możliwie jak najmniejszej ilości płytek, ale przy tym na tyle dużej, aby proces montażu był optymalny czasowo. Wraz ze wzrostem liczby obwodów w panelu, frezowanie usuwa coraz więcej materiału, pogarszając jego stabilność. W efekcie może się on uginać podczas produkcji i montażu, albo nawet rozłamać zanim trafi do odbiorcy.
Dla uzyskania jak największej sztywności panelu konieczne jest zastosowanie odpowiedniej liczby mostków trzymających pojedyncze płytki w panelu. Przyjmuje się, że na każde 50 mm krawędzi obwodu stosuje się minimum jeden mostek. Większa liczba mostków wskazana jest przy skomplikowanych kształtach oraz cieńszych laminatach. Nieprawidłową praktyką jest projektowanie wyłącznie dwóch mostków tylko na poziomych lub pionowych krawędziach (rys. 4). W takiej wadliwej konfiguracji mostków dla dużej liczby płytek w rzędzie, połączonych ze sobą jedynie na dwóch krawędziach, istnieje niebezpieczeństwo rozłamania panelu podczas produkcji. Cienki fragment laminatu naddaje się znacznie łatwiej frezowi, w wyniku tego wymiary końcowe pojedynczych płytek są inne niż oczekiwane. Krawędzie pozbawione trzymania zaś mogą okazać się nierówne.
Istnieją jednak sytuacje w których należy unikać nadmiernej liczby mostków. Zwiększają one sztywność konstrukcji panelu, wydłużają jednak czas i koszt frezowania. Wynika to z faktu, że zasadniczy wpływ na trwanie procesu ma liczba wejść frezu w materiał, na co z kolei bezpośredni wpływ ma ilość zastosowanych mostków.
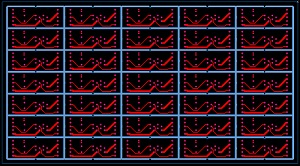
(a)
.jpg)
(b)
Rys. 4. Widok niestabilnego panelu (a), w którym zastosowano po 2 mostki na poziomych krawędziach płytki (b)
Nie bez znaczenia na sztywność panelu oraz jakość krawędzi obwodów po depanelizacji ma wybór typu mostków.
Wyróżniania się 3 rodzaje mostków: bez perforacji, z perforacją oraz rylcowane.
Zastosowanie mostków bez perforacji (fot. 5a) jest najkorzystniejszym rozwiązaniem gwarantującym stabilność panelu oraz jakość krawędzi po wyłamaniu płytki. Jego separacja możliwa jest tylko za pomocą frezarki. Najbardziej popularne są mostki z perforacją (fot. 5b), zapewniające optymalną stabilność przy stosunkowo łatwej depanelizacji. Ich wadą są pozostałości po wyłamaniu wystające poza obrys obwodu oraz nierówne krawędzie w okolicy mostków (fot. 5c). Te negatywne zjawisko można redukować przesuwając otwory perforacji w głąb obwodu. Jednakże trzeba pamiętać o zachowaniu odpowiedniej odległości perforacji od mozaik, aby te nie zostały uszkodzone z powodu naprężeń powstałych podczas wyłamywania płytek z panelu. Mostki rylcowane mogą być zastosowane wyłącznie na krawędziach poziomych i pionowych. Ich zaletą jest łatwość separacji, jednoczesne frezowanie i rylcowanie tych samych krawędzi podwyższa jednak niepotrzebnie koszty obróbki mechanicznej. Ponadto w jej wyniku powstają „włosy” laminatu mogące niekiedy utrudniać proces montażu.
.jpg)
(a)

(b)
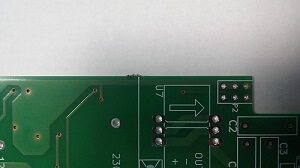
(c)
Fot 5. Mostki frezowane bez perforacji (a), z perforacji (b), pozostałości po wyłamaniu płytek z panelu (c).
Panel frezowany powinien posiadać dodatkową ramkę wokół krawędzi w celu zwiększenia stabilności całej konstrukcji. Jej minimalna szerokość to 7 mm. Aby uzyskać taką ramkę, konieczny jest pas laminatu o szerokości 9 mm (od krawędzi obwodów do krawędzi panelu). Różnica w szerokości - 2 mm, przeznaczona jest na przejścia frezu. Typowa szerokość ramki to 8÷10 mm. Im ramka jest szersza tym sztywność panelu jest większa. Dodatkowo dla jego wzmocnienia nie wykonuje się perforacji mostków od strony ramki.
Standardowy frez używany przez producentów obwodów, w tym TS PCB Techn-Service S.A., ma średnicę 2 mm. Taka powinna być minimalna odległość pomiędzy płytkami, zapewni ona optymalną tolerancję ich wymiarów i wykończenie krawędzi przy możliwie krótkim procesie frezowania. Możliwe jest zastosowanie mniejszych odległości i co za tym idzie frezów. Jednakże pogorszy to sztywność panelu i może prowadzić do niezachowania zakładanej tolerancji wymiarowej obwodu. Poza tym mniejsze frezy wymagają obniżenia posuwu, co bezpośrednio przekłada się na wydłużenie procesu oraz zwiększenie jego ceny.
Aby zwiększyć sztywność panelu, szczególnie przy obwodach o niewielkich rozmiarach, celowo zwiększa się odległości pomiędzy płytkami co najmniej do 9 mm (po 2 mm na narzędzie i 5 mm ramki trzymającej płytki). Najczęściej wystarczające jest zachowanie większych odległości pomiędzy wierszami (fot. 6) lub kolumnami. Dodatkowe pasy laminatu wraz z ramką panelu tworzą wówczas stabilną konstrukcję dla pojedynczych płytek pozwalająca na bezpieczną produkcję, transport oraz montaż obwodów. Rozsunięcie obwodów na mniejsze odległości prowadzi do powstawania ramki o szerokości 1÷2 mm, znacząco pogarsza to sztywność panelu.
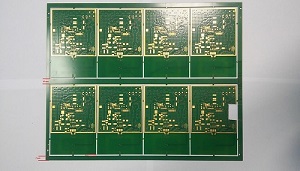
Fot. 6. Stabilny panel frezowany z ramką i marginesem pomiędzy płytkami.
Wadą obróbki frezowaniem jest duża powierzchnia odpadów. Przy zastosowaniu odległości większych niż 2 mm pomiędzy pojedynczymi płytkami, odpad to nawet 50% powierzchni całego panelu. Frezowanie jest też droższym procesem niż rylcowanie. Zapewnia jednak osiągnięcie tolerancji wymiarowej na poziome nawet ±0,05 mm przy bazowaniu obrabiarki CNC na mozaice. Krawędź rylcowana w przekroju poprzecznym tworzy trójkąt, podczas gdy krawędź frezowana jest prosta i gładka, bez zbędnych pozostałości laminatu czy nitek tworzywa (fot. 7).
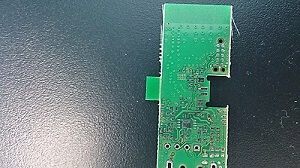
fot.7. Pozostałości laminatu