Ślepe i zagrzebane przelotki - jak wykorzystać ich zalety w projektach urządzeń elektronicznych
25.11.2016
Płytki drukowane we współczesnej elektronice stają się coraz bardziej skomplikowane, bo na coraz mniejszej powierzchni projektanci muszą umieścić coraz więcej podzespołów. Rozwiązaniami umożliwiającymi miniaturyzację przy jednoczesnym wzroście złożoności urządzeń, są ślepe i zagrzebane przelotki, które od lat są w ofercie firmy Techno-Service. Aby móc w pełni wykorzystać możliwości przelotek, warto wiedzieć o nich nieco więcej - czym różnią się ich poszczególne typy, jak prawidłowo zaprojektować zawierające je obwody oraz jakie korzyści uzyskuje się dzięki tak zaprojektowanym układom.
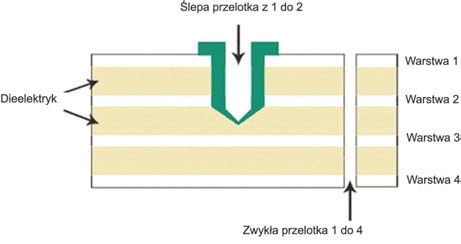
Rys. 1. Schemat płytki ze ślepymi przelotkami z warstwy 1 do warstwy 2
Terminologia dotycząca nowych rozwiązań technologicznych jest bardzo rozległa. Jednym z głównych pojęć jest ślepa przelotka (blind via). Jest to otwór, który zaczyna się na powierzchni płytki, ale nie przechodzi na drugą stronę PCB. Otwory te mogą być wiercone mechanicznie lub z wykorzystaniem lasera. Blind via łączy warstwę powierzchniową płytki (top lub bottom) z wewnętrzną powłoką bez przechodzenia przez całą płytkę.
W praktyce widać również coraz liczniejsze używanie przy projektowaniu PCB zagrzebanych przelotek (buried via). Płytki ze ślepymi przelotkami wykorzystywane są w sytuacji, gdy zaprojektowany układ jest bardzo gęsto upakowany i projektant potrzebuje więcej miejsca na jednej ze stron płytki (top lub bottom) lub tego miejsca na jednej ze stron mu brakuje, a nie ma potrzeby projektowania połączenia w płytce pomiędzy wszystkimi jej warstwami (through hole).
Produkcja płytek ze ślepymi bądź zagrzebanymi przelotkami znacząco różni się od procesu wytwarzania standardowych obwodów. Płytki ze ślepymi przelotkami wykonuje się tak jak zwykłe wielowarstwowe do etapu wiercenia. Mają one dodatkowe otwory, które łączą ze sobą tylko dwie warstwy w płytce czterowarstwowej.
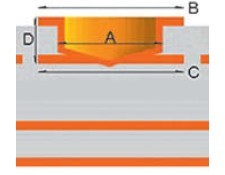
Rys. 2. Otwór ślepej przelotki (min. otwór wiercony A = 0,15 mm, min. średnica padu warstw zewnętrznych B = 0,25 mm,
min. średnica padu warstw wewnętrznych C = 0,25 mm, skala D:A = 1:1)
Otwory te nie są do końca przewiercone, stąd nazwa ślepe przelotki. Poprzez wywiercenie otworów na głębokość, na której znajduje się warstwa miedzi wewnątrz płytki, możemy uzyskać, po nałożeniu metalizacji, połączenie elektryczne pomiędzy tylko dwiema warstwami. Zwiększa to znacznie możliwości płytek i ich zastosowania.
Takie rozwiązanie ma liczne zalety: zwiększoną gęstość upakowania elementów SMT (przelotki nie zajmują wszystkich warstw) oraz bezpieczeństwo produktu wynikające z jakości izolacji elektrycznej. Wcześniej czy później każdy konstruktor płytek wielowarstwowych spotyka się z koniecznością użycia otworów, które nie przechodzą przez płytę na wskroś. Niestety nie wypracowano jednolitych standardów projektowania i wykonania tego typu przelotek.
Możliwości ich wykonania uzależnione są od rozwiązań technologicznych, stosowanych przez konkretnego producenta obwodów wielowarstwowych. Mimo to można spróbować wyodrębnić pewne ogólne zasady, które pozwolą zaprojektować obwód w ten sposób, że będzie on do wykonania w nieomalże dowolnym, nowoczesnym zakładzie produkującym wielowarstwowe PCB.
Jak projektować?
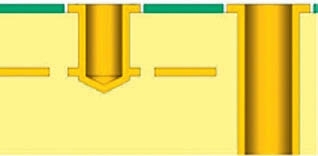
Rys. 3. Blind via z nałożoną metalizacją
W momencie, gdy konstruktor zaczyna projektować obwód wielowarstwowy, pierwszym jego krokiem powinien być wybór budowy obwodu wielowarstwowego. Decyzja odnośnie do wyboru budowy wielowarstwowej powinna być podjęta już na samym początku procesu projektowania, a jeszcze przed rozpoczęciem tego procesu założenia powinny być skonsultowane z producentem obwodu.
Nieraz podczas projektowania otworów w wielowarstwowych płytkach konstruktor bierze pod uwagę jedynie własne wyobrażenie, nie uwzględniając możliwości technologicznych producenta lub też dodaje przelotki w biegu, dostosowując je do potrzeb już prawie "sprasowanego" projektu, gdy zabraknie na nim miejsca.
Konsekwencje mogą być dotkliwe, zarówno dla samego konstruktora, który ostatecznie może być zmuszony do przeprojektowania całego obwodu, jak i całej firmy - nieunikniona jest strata pieniędzy i czasu, związana z poszukiwaniami odpowiedniego producenta, zwiększeniem kosztu zlecenia i wydłużeniem czasu jego realizacji. Zdarza się, że przygotowany w nieprzemyślany sposób projekt jest z definicji nie do wykonania, w żadnym z istniejących na świecie zakładów lub też wartość realizacji samego obwodu przewyższa budżet przewidziany na cały projekt.
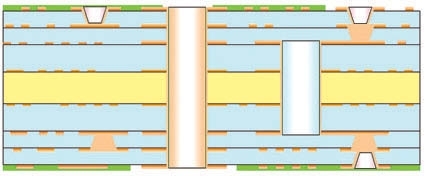
Rys. 4. Buried via i blind via
Podsumowując, przy planowaniu budowy obwodu drukowanego głównym zadaniem konstruktora jest optymalne połączenie wymogów samego urządzenia z możliwościami technologicznymi producenta. Dobór materiałów i grubości warstw to oddzielny, złożony temat. Celem producentów obwodów jest określenie takich zasad konstrukcji obwodu, które umożliwią jego produkcję. Dlatego też warto przeanalizować metody projektowania przelotek, które nie przechodzą przez płytę na wskroś.
Ślepe przelotki w obwodach wielowarstwowych przeznaczone są do łączenia zewnętrznych warstw sygnałowych z jedną lub kilkoma warstwami wewnętrznymi. Wiercenie ślepych przelotek na żądaną głębokość ma swoje technologiczne ograniczenia. Aby zapewnić odpowiednią jakość metalizacji, konieczny jest odpowiedni dobór wymiarów przelotki: ważne, by H/d (stosunek głębokości odwiertu do średnicy otworu) nie wyniósł więcej niż 1, optymalnie 0,8. Oznacza to, że im głębsza przelotka i dielektryczny odstęp pomiędzy warstwami, tym większa powinna być średnica przelotki.
W trakcie projektowania obwodu wielowarstwowego należy uwzględnić, że podczas metalizacji otworów zagrzebanych na powierzchni konkretnej warstwy dochodzi do osadzenia miedzi (25-45 dodatkowych mikrometrów). Dlatego też, przy planowaniu minimalnej, dopuszczalnej grubości ścieżki, na takich warstwach należy wziąć pod uwagę dodatkową metalizację.
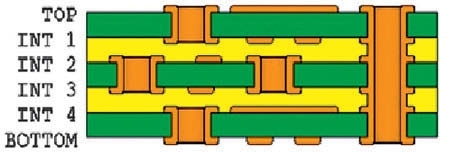
Rys. 5. Zagrzebane i ślepe przelotki w płytce 6-warstwowej
Technologia wykonania tego typu przelotek podobna jest do technologii wykonania zwykłych metalizowanych przelotek, z późniejszym wypełnieniem przelotek pastą i sprasowaniem w kompletnym pakiecie obwodu wielowarstwowego. Należy dodać, że wykonanie mikroprzelotek bezpośrednio nad zagrzebaną przelotką nie jest możliwe, ponieważ w tym miejscu nie ma zwartej powierzchni, a jest miedziany pierścień z otworem w środku.
Sposób wykonania tego typu struktury jest następujący: najpierw należy przewiercić na wylot i nanieść metalizację na każdy z rdzeni, następnie nanosi się obraz mozaiki na wewnętrznych powierzchniach rdzeni i przeprowadza się prasowanie pakietu wielowarstwowego. Z punktu widzenia produkcji taka konstrukcja procesu technologicznego nie jest optymalna, ponieważ wymaga dodatkowych etapów związanych z metalizacją. Jednak, jeżeli zakład nie dysponuje parkiem maszynowym, który umożliwia wiercenie mikroprzelotek, jest to jedyna metoda produkcji tego typu otworów.
Wariacje liczby warstw w obwodzie wielowarstwowym z zagrzebanymi przelotkami mogą być różne, jednak nie należy przesadzać ani ze złożonością samego obwodu, ani z liczbą zagrzebanych i ślepych przelotek. Jeżeli można wybrać pomiędzy kolejnym nieprzelotowym otworem a dodatkową parą warstw, to lepiej zdecydować się na dodatkowe warstwy. Szczególnie w przypadku układów scalonych z BGA z rastrem 1,0 mm i nawet 0,8 mm nie ma konieczności stosowania nieprzelotowych otworów. W przypadku obwodów z BGA z rastrem 0,65 mm i 0,5 mm niestety dla otworów nieprzelotowych nie ma alternatywy. W każdym z wypadków budowa obwodu wielowarstwowego powinna być zawczasu skonsultowana z producentem.
Podsumowanie
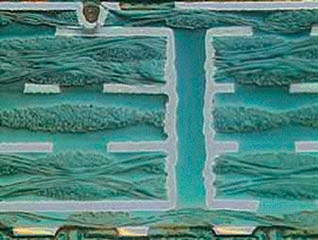
Rys. 6. Przekrój płytki z zagrzebaną przelotką
Zastosowanie w konstrukcjach płytek mikrootworów i otworów nieprzelotowych łączących kilka warstw obwodu oraz otworów wewnętrznych umożliwia kilkakrotny wzrost gęstości połączeń bez zwiększania liczby warstw. Tak zbudowane płytki są znacząco tańsze od równoważnych pod względem gęstości połączeń płytek standardowych z otworami przelotowymi. Przykładowa płytka 4-warstwowa z mikrootworami nieprzelotowymi umożliwia uzyskanie gęstości połączeń odpowiadającej 10-warstwowej płytce z otworami przelotowymi. Cena płytki 10-warstwowej będzie o 100-150% większa od płytki 4-warstwowej wykonanej w technologii HDI (High Density Interconnection).
Kosztowne i trudne zadanie wytworzenia obwodów ze ślepymi czy zagrzebanymi przelotkami daje możliwości rozwoju urządzeń elektronicznych, zapewnia również bardziej stabilną pracę układów i lepszą ich wydajność. Chociaż kiedyś obawiano się nowinek technologicznych i były one bardzo drogie, najnowsze badania i postępy w tym zakresie pozwalają wyeliminować niemal wszystkie problemy. W rzeczywistości ślepe i zagrzebane przelotki zdają się coraz bardziej dominować w płytkach o wysokiej technologii, ponieważ zapewniają dużą gęstość upakowania elementów na płytce, co jest bardzo opłacalną alternatywą dla przelotek konwencjonalnych.