Budowa, właściwości i projektowanie wielowarstwowych obwodów drukowanych
25.11.2015
Od współczesnych urządzeń elektronicznych oczekuje się dużej funkcjonalności, niewielkich rozmiarów oraz wysokiej niezawodności. Takie cechy osiąga się dzięki dużej liczbie zintegrowanych i zminiaturyzowanych układów scalonych powiązanych skomplikowanymi sieciami połączeniowymi. Odwzorowanie ich na typowym dwustronnym obwodzie drukowanym nie jest możliwe m.in. ze względu na pożądane ograniczone rozmiary samego obwodu, stąd konieczne staje się zastosowanie obwodów wielowarstwowych, niekiedy o wysokiej gęstości upakowania HDI (High Density Interconnect), mających typowo 4, 6, 8 lub więcej warstw przewodzących (mozaik). W artykule przedstawiono informacje przybliżające zagadnienia budowy, wytwarzania oraz technik prawidłowego projektowania obwodów wielowarstwowych. Przestrzeganie ich pozwoli uniknąć problemów już na etapie projektowania stosu oraz podczas późniejszej produkcji obwodów.
Struktura obwodów wielowarstwowych
W odróżnieniu od obwodów dwustronnych konstrukcja laminatów wielowarstwowych jest znacznie bardziej złożona i ma formę stosu (stack-up, build-up) o uporządkowanej strukturze warstwowej, zwykle symetrycznej względem środka. W przekroju poprzecznym takich laminatów występują trzy elementy: folie miedziane oraz rdzenie i prepregi, które wykonane są najczęściej z laminatu FR4. Wzajemne ułożenie tych elementów ściśle określa norma IPC-2222 opisująca dwa rodzaje ułożenia stosu wielowarstwowego: typ 1 oraz typ 2. Oba rodzaje ułożenia warstw dla przykładowego obwodu 4-warstwowego przedstawiono na rys. 1.
.jpg)
Rys. 1. Układ warstw obwodu 4-warstwowego dla typu 3 (a) i typu 4 (b)
Stos oznaczony jako typ 3 spotykany jest sporadycznie i wykorzystywany do produkcji nieskom plikowanych projektów. Wykonanie w tym układzie przelotek łączących przewodzące warstwy wewnętrzne (przelotki zagrzebane) nie jest możliwe, a przelotek nieprzechodzących na wskroś (przelotki ślepe) jest skomplikowanym procesem technologicznym. Jedyną zaletą stosu typu 3 jest nieco większa sztywność w porównaniu z typem 4 dla tej samej grubości laminatu, szczególnie dla projektów o bardzo zróżnicowanych powierzchniach miedzi warstw przewodzących.
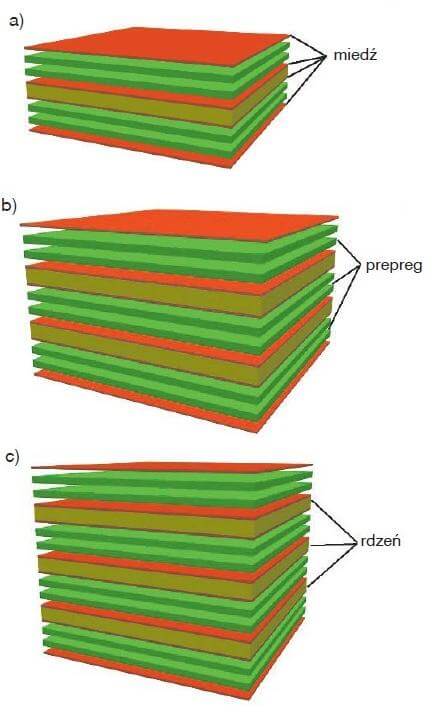
Rys. 2. Przekroje poprzeczne obwodów 4- (a), 6- (b) i 8- warstwowych (c)
Najbardziej rozpowszechnionym układem warstw laminatów wielowarstwowych, predestynowa nym do produkcji skomplikowanych projektów, jest typ 4. Jest stosowany przez wielu producentów PCB, w tym przez TS PCB. Umożliwia wykonanie przelotek zagrzebanych na rdzeniach oraz stosunkowo proste wiercenie przelotek ślepych. Ponadto, z uwagi na możliwość łączenia ze sobą prepregów, o różnej grubości, typ 4 zapewnia dużą elastyczność kształtowania grubości zarówno warstw prepregów jak i całkowitej laminatu. Z tych powodów dalsza część artykułu poświęcona będzie obwodom wielowarstwowym o typie 4.
Przykładowe stosy obwodów 4-, 6- i 8-warstwowych przedstawiono na rys. 2. Z rysunku widać, że wnętrze stosu zawiera rdzenie składające się z dielektryka pokrytego obustronnie folią miedzianą, o strukturze laminatu dwustronnego, które tworzą przewodzące warstwy wewnętrzne obwodów wielowarstwowych. Najbardziej skrajne zewnętrzne warstwy stosu stanowią folie miedziane z odwzorowanymi mozaikami warstw top i bottom. Rdzenie i folie Cu rozdzielone są prepregami, których zadaniem jest mocne i trwałe sklejenie stosu w całość przy zachowaniu odpowiednich odległości między nimi.
Materiały do budowy obwodów wielowarstwowych
Parametry elementów składowych stosów wielowarstwowych, a w szczególności ich grubości, są znormalizowane. Poniżej przedstawione zostaną dane katalogowe najczęściej wykorzystywanych prepregów, rdzeni i folii miedzianych.
Prepregi produkowane są jako pojedyncze włókna szklane nasycone niezupełnie spolime ryzowaną żywicą epoksydową. Podczas procesu prasowania, w wyniku wysokiej temperatury oraz ciśnienia, rozpływają się one, sklejając poszczególne warstwy stosu pomiędzy sobą. Na rynku dostępnych jest wiele typów prepregów o różnych grubościach oraz zawartości żywicy.
.jpg)
Tab. 1. Parametry najczęściej stosowanych prepregów
Jednakże większość producentów obwodów ma w swojej ofercie 3-4 rodzaje (tab. 1) gwarantujące odpowiednie parametry jakościowe obwodów oraz optymalną elastyczność w konstruowaniu stosów. Takie postępowanie jest uwarun kowane głów nie względami ekonomicz nymi. Prepregi charakteryzują się stosunkowo krótkim terminem przydatności, więc utrzymywanie w magazynie wielu różnorodnych prepregów narażałoby producenta PCB na duże straty, ze względu na konieczność odświeżania wielu typów, zwłaszcza o niskiej popularności.
.jpg)
Tab. 2. Parametry popularnych rdzeni
Jak już wspomniano, rdzenie są laminatami dwustronnymi pokrytymi miedzią o typowych grubościach: 18, 35 (standard), 70 i 105 µm. Analogicznie jak w przy padku prepregów, grubości rdzeni, które uwzględniają grubość folii Cu, są unormowane i tworzą typoszereg. Dostępne typowe grubości rdzeni oraz wykorzystane do ich budowy prepregi przed stawiono w tab. 2.
Producenci PCB, podobnie jak w przypadku prepregów, dysponują kilku nastoma najbardziej popularnymi rdzeniami, także z różnymi grubościami folii miedzianej oraz w wersjach z podwyższonym parametrem Tg (150 i 180oC). Folie miedziane mają grubości uszeregowane w sposób analogiczny do rdzeni tj.: 18, 35, 70 i 105 µm. Umożliwiają one po procesie metalizacji uzyskanie następujących końcowych grubości miedzi: 35 (standard), 70, 105 i 140 µm.
Zasady konstruowania obwodów
Proces projektowania stosu wielowarstwowego polega na takim dobraniu parametrów elemen tów składowych, które zagwarantują zakładane właściwości elektryczne (prądy, impedancje, odporność na przebicia) i mechaniczne (grubość, sztywność, łatwość obróbki) laminatu. Oznacza ono wyselek cjonowanie parametrów:
- rdzeni w celu uzyskania pożądanej liczby warstw, odległości pomiędzy warstwami wewnętrznymi umieszczonymi w obrębie pojedynczych rdzeni oraz grubości przewodzących warstw wew nętrznych,
- prepregów zapewniających odpowiednie odległości pomiędzy rdzeniami, rdzeniami i zewnętrz nymi warstwami mozaik przy wystarczającym wypełnieniu żywicą,
- folii miedzianych z uwzględnieniem parametrów DRC zewnętrznych mozaik obwodu.
Konstrukcja stosu wielowarstwowego już na etapie projektowania powinna uwzględniać możliwości technologiczne oraz wachlarz materiałów, jakimi dysponuje producent PCB. Zastosowanie wyszukanych rdzeni i prepregów oraz ich nietypowego wzajemnego układu może w skrajnych przypadkach uniemożliwić produkcję obwodu.
Zwykle w takich sytuacjach producent proponuje alternatywne budowy o parametrach jak najbardziej zbliżonych do pierwotnej, lecz wykorzystujące materiały, jakie ma. Forsowanie wykonania stosu z nietypowych materiałów na pewno zwiększy czaso- i kosztochłonność realizacji projektu z uwagi na konieczność ich zamówienia, o ile nie występują inne przesłanki technologiczne wykluczające możliwość produkcji.
Zaleca się, w miarę możliwości, stosowanie stosów symetrycznych względem środka przekroju poprzecznego, aby uzyskać zbliżone naprężenia powierzchniowe z obu stron laminatu. Sugestia ta dotyczy także rozkładu powierzchni miedzi na mozaikach, szczególnie warstw wewnętrznych. Niekiedy wykonanie symetrycznej budowy jest niemożliwe, np. ze względu na określone impedancje linii transmisyjnych, co może powodować wichrowanie się gotowych obwodów podczas montażu (lutowania).
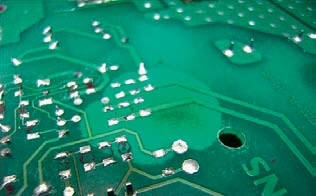
Rys. 3. Przykład delaminacji
Przy konstruowaniu stosu należy przestrzegać reguły stosowania co najmniej dwóch prepregów oddzielających sąsiednie warstwy przewodzące. Użycie pojedynczego może doprowadzić do powstania upływności prądów oraz powstania ognisk delaminacji, ponieważ podczas prasowania płytki włókna szklane mogą ulegać uszkodzeniu, szczególnie na krawędziach elementów mozaik.
Liczba oraz rodzaj zastosowanych prepregów jest kluczowa z punktu widzenia wypełnienia żywicą obszarów pomiędzy warstwami przewodzącymi i uzależniona od grubości warstw przewodzących oraz od ich wypełnienia miedzią. Niewystarczające wypełnienie żywicą wywołuje zjawisko niedoboru żywicy (resin hunger), powodujące powstawanie pustych przestrzeni pomiędzy warstwami , które mogą prowadzić do rozwarstwienia i delaminacji (rys. 3). Mogą one również stać się ogniskiem korozji lub upływności prądu wskutek uwięzienia w nich produktów procesu galwanizacji.
Najlepszym sposobem sprawdzenia wymaganej ilości żywicy jest zastosowanie specjalnych programów do projektowania i kontroli stosów wielowarstwowych, które w wersji darmowej są dostępne na stronach internetowych renomowanych producentów laminatów. Najczęściej spotykanymi programami są Multical (Isola) oraz Multilayer Architect (Technolam).
Obok przedstawiono porównanie stosów o prawidłowym (rys. 4a) i niewystarczającym wypełnieniu żywicą (rys. 4b) opracowanych w programie Multical. Problem braku żywicy można rozwiązać na kilka sposobów: zwiększyć powierzchnię miedzi na warstwach wewnętrznych, zastosować prepreg o większej zawartości żywicy (z oznaczeniem MR lub HR) lub zastosować dodatkowy prepreg, co niestety wiąże się z powiększeniem grubości dielektryka i w efekcie całego laminatu.
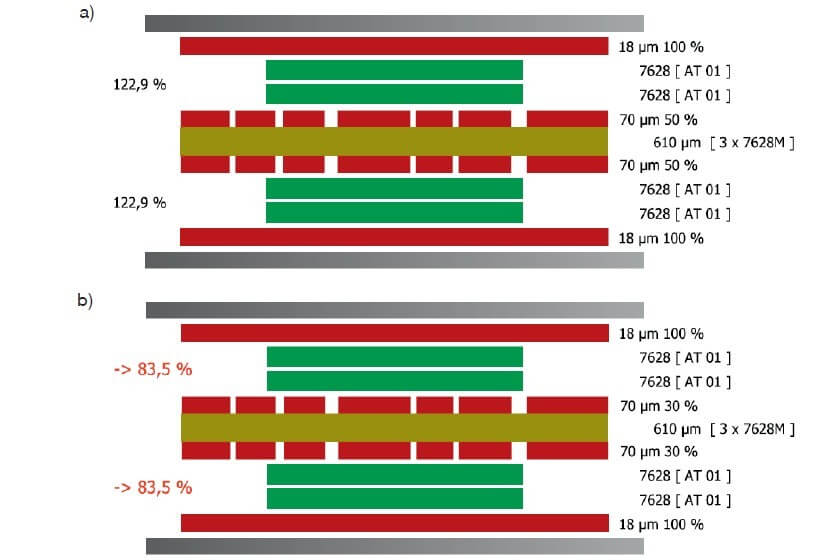
Rys. 4. Widok budowy z prawidłowym (a) i zbyt małym (b) poziomem żywicy w programie Multical
Innym walorem użytkowania tego typu programów jest możliwość dokładnego, w stosunku do zwykłych wyliczeń matematycznych, określania odległości pomiędzy warstwami oraz grubości końcowej laminatu po sprasowaniu. Porównanie odległości warstw przykładowego stosu obwodu 4-warstwowego określone drogą obliczeń, wyznaczenia w programie Multical oraz pomierzone na podstawie obrazu mikroskopowego zgładu (szlifu poprzecznego, mikrosekcji) wyprodukowanego obwodu przedstawiono na rys. 5.
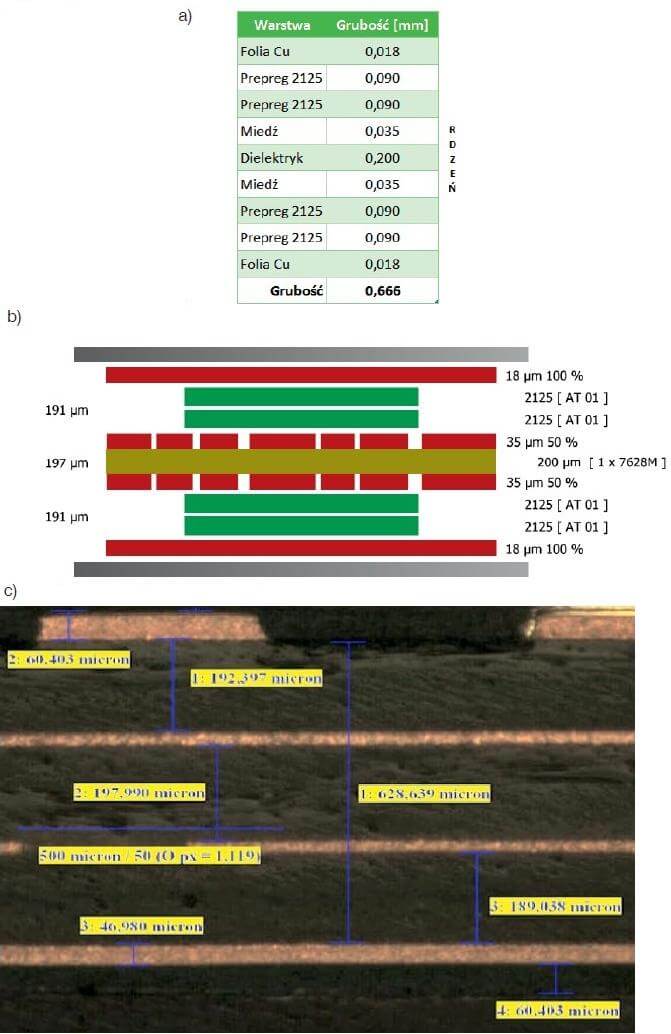
Rys. 5. Porównanie grubości warstw obliczonych (a), wyznaczonych w programie Multical (b) oraz pomierzonych w rzeczywistym obwodzie 4-warstwowym (c)
Dla tego obwodu projektant założył, że odległości pomiędzy warstwami muszą wynosić 180 µm. W tym celu, na podstawie tab. 1, zastosował dwa prepregi 2125. Jednakże podczas projektowania przy użyciu programu Multical, który uwzględnia wartości powierzchni miedzi na warstwach wewnętrznych oraz zawartość żywicy w prepregach, widać, że łączna grubość dwóch prepregów 2125 jest o około 10 µm większa.
Wyniki wykonanej mikrosekcji rzeczywistego obwodu potwierdziły, że grubość dielektryka to ok. 190 µm, co jest wartością bardzo zbliżoną do uzyskanej w Multicalu. Uzyskanie pełnej zgodności grubości warstw prepregów oraz rdzeni z wartościami uzyskanymi w Multicalu jest mało prawdopodobne ze względu na tolerancję grubości tych materiałów.
Niektóre projekty układów elektronicznych, np. pracujące z wysokimi napięciami, wymagają zastosowania rdzeni o grubościach powyżej 1 mm. Tego typu rdzenie najczęściej nie są dostępne u producentów PCB, ze względu na małą popularność. Istnieje jednak możliwość ich uzyskania drogą pośrednią przez prasowanie dwóch cieńszych rdzeni rozdzielonych prepregami. Rdzeń w takim przypadku ma strukturę stosu typu 3, ale ze strawioną warstwą miedzi położoną wewnątrz. Przykładowy stos obwodu z rdzeniem o grubości 1,6 mm przedstawiono na rys. 6.
W celu zwiększenia gęstości upakowania elementów obwodów wielowarstwowych dla założonej liczby warstw wykorzystuje się przelotki zagrzebane i ślepe. Jak już wspomniano, przelotki zagrzebane umożliwiają połączenie mozaik w obrębie pojedynczych rdzeni i nie potrzebują powierzchni na warstwach zewnętrznych, która może zostać wykorzystana np. do montażu elementów. Warto pamiętać, że istnieje ograniczenie maksymalnej średnicy przelotek zagrzebanych wynikające z możliwości powstawania ognisk delaminacji. Producent TS PCB zaleca stosowanie przelotek zagrzebanych o średnicach nie większych niż 1,5 mm.
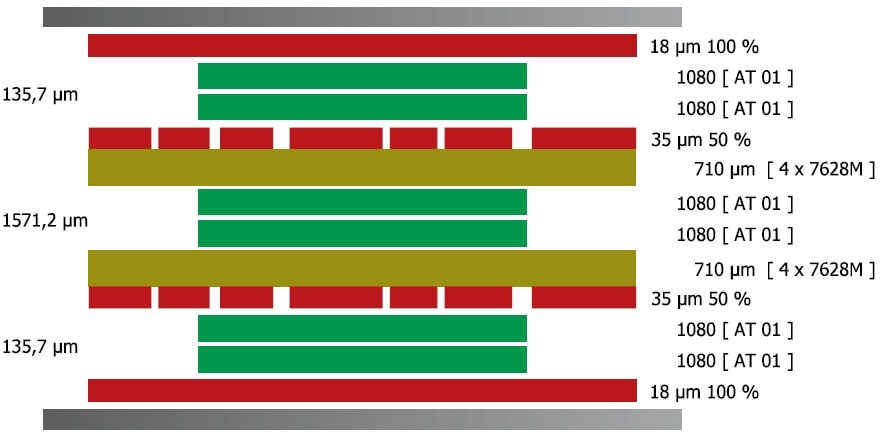
Rys. 6. Przykładowy stos z rdzeniem 1,6 mm
Przelotki ślepe umożliwiają połączenie jednej z zewnętrznych warstw przewodzących z jedną lub kilkoma warstwami wewnętrznymi. Dzięki temu, w porównaniu ze zwykłą przelotką, uzyskuje się wolne miejsce na przeciwległej warstwie zewnętrznej, które można wykorzystać np. na poprowadzenie sieci połączeniowych.
Pewnym ograniczeniem ślepych przelotek jest zależność ich średnicy od dopuszczalnej głębokości wiercenia i w efekcie możliwej liczby warstw do połączenia. Redukcji rozmiarów ślepych przelotek sprzyja jak najmniejsza odległość pomiędzy łączonymi warstwami. Zaleca się, o ile nie występują inne przeciwwskazania, ich stosowanie na możliwie cienkich laminatach, o grubości poniżej 1 mm.
Jeśli potrzebna jest większa grubość materiału, to warto tak zaprojektować obwód, aby ślepe przelotki łączyły tylko warstwy zewnętrzne z najbliższymi wewnętrznymi, warstwy takie oddzielić dwoma prepregami 1080, a oczekiwaną grubość końcową laminatu uzyskać przez zastosowanie grubszych rdzeni.
Podsumowanie
W artykule omówiono budowę stosów wielowarstwowych, parametry wykorzystywanych materiałów oraz zasady prawidłowego konstruowania obwodów. Przedstawiono narzędzia ułatwiające proces projektowania stosów oraz gwarantujące uzyskanie prawidłowego wypełnienia żywicą pożądanej końcowej grubości zarówno warstw prepregów oraz całego laminatu. Zastosowanie się do wymienionych zasad pozwoli uniknąć wielu problemów związanych z produkowaniem i montażem tego typu obwodów oraz związanych z nimi dodatkowych kosztów.