Dokumentacja produkcyjna obwodów drukowanych – jak jest tworzona oraz co zawiera?
08.02.2016
Projektując układ elektroniczny, konstruktor kieruje się wizją obwodu drukowanego o sieci połączeń gwarantującej jego bezawaryjne i prawidłowe działanie. Opracowany projekt w wersji elektronicznej w programie CAD oraz wygenerowana dokumentacja projektowa przeznaczona dla producenta obwodów drukowanych są odzwierciedleniem tej wizji. Na tej bazie tworzona jest właściwa dokumentacja produkcyjna wykorzystywana na poszczególnych etapach produkcji PCB. Elementy składające się na wyżej wymienioną dokumentację to m.in. programy obróbki mechanicznej projektu (wiercenie, frezowanie i rylcowanie) dla maszyn CNC, klisze odwzorowujące poszczególne warstwy obwodu (mozaiki, maski antylutownicze, opisy), a także programy do testowania optycznego i elektrycznego.
W niniejszym artykule omówiony zostanie proces opracowywania dokumentacji produkcyjnej, a także kolejność i opisy poszczególnych etapów produkcyjnych.
Projekt i technologia wykonania
Na rynku występuje duża różnorodność oprogramowania CAD wspierającego tworzenie projektów obwodów. Upowszechnionym standardem przechowywania dokumentacji projektowej są formaty Gerber RS274-X oraz ODB++, które akceptowane są przez większość renomowanym producentów PCB. Większość programów, w tym najbardziej popularne (Altium Designer, Protel, Eagle), posiadają możliwość eksportu danych do ww. formatów
Dokumentacja projektowa musi być przede wszystkim kompletna i nie może powodować trudności w interpretacji oczekiwań konstruktora. Należy pamiętać o jednoznacznym i zwięzłym nazewnictwie plików oraz usuwaniu zbiorów niemających związku z produkcją obwodu, jak np. plików dla montażu. Oprócz plików projektu, dokumentacja musi zawierać specyfikację technologii wykonania PCB. Stanowi to niezwykle istotny element dokumentacji produkcyjnej określający: wymagane do produkcji materiały, kolejność poszczególnych procesów technologicznych i ich parametry. Pozornie drobne uchybienia w zapisach technologii, np. zbyt ogólne informacje lub ich brak, mogą doprowadzić do wyprodukowania płytek drukowanych niezgodnych z pierwotnymi założeniami projektanta. Niestety najczęściej skutki niewłaściwego sformułowania technologii projektu są nieodwracalne. Tylko nieliczne parametry technologii można skorygować już podczas produkcji, dlatego niewielu producentów, w tym TS PCB, dopuszcza wprowadzanie korekt.
Obróbka CAM
Pierwszym etapem poprzedzającym produkcję jest weryfikacja wykonalności obwodu drukowanego i dostosowanie go do wymagań oraz parametrów procesów. Dzięki wprowadzeniu do projektu modyfikacji sugerowanych przez producenta PCB możemy ostatecznie uzyskać obwód
wysokiej jakości, który jest zgodny z zamysłem projektanta i normami IPC. Najczęściej proponowane zmiany dotyczą:
wysokiej jakości, który jest zgodny z zamysłem projektanta i normami IPC. Najczęściej proponowane zmiany dotyczą:
- powiększenia pierścieni wokół otworów lub dodania łezek dla ochrony ciągłości połączeń na granicy przelotka – ścieżka,
- zachowania minimalnej odległości miedzi od krawędzi, która zagwarantuje odpowiednią izolację elektryczną oraz zapobiegnie jej uszkodzeniu podczas obróbki mechanicznej,
- doboru prawidłowych wielkości odsłonięć na masce antylutowniczej, aby nie nachodziła na pady,
- poszerzenia ścieżek o współczynnik trawienia dla zapewnia odpowiedniej ich szerokości,
- pogrubienia linii opisowych do minimalny wartości, a także przycięcia linii nachodzących na pady oraz leżących poza obrysem płytki,
- korekty średnic otworów, aby wykonać je w odpowiedniej tolerancji.
W profesjonalnej produkcji obwodów drukowanych wykorzystywane są tzw. formaty produkcyjne, czyli duże płaty laminatu o ustandaryzowanych rozmiarze dostosowanym do całego ciągu technologicznego. Przygotowując produkcję inżynier CAM na dostępnym polu roboczym danego formatu rozmieszcza poszczególne warstwy pojedynczej płytki lub panelu tak, aby optymalnie wykorzystać jego powierzchnię. Następnie na ramkach formatów, czyli poza obszarem roboczym, umieszczane są otwory bazowe umożliwiające prawidłowe zamocowanie formatów na poszczególnych maszynach. Działanie to ułatwia produkcję oraz zwiększa jej powtarzalność i efektywność.
Odwzorowanie warstw przewodzących
Klisze warstw przewodzących są podstawowym składnikiem dokumentacji produkcyjnej. W celu odwzorowania mozaik połączeń powszechnie wykorzystuje się fotochemiczną metodę subtraktywnego strawiania zbędnych obszarów miedzi. W procesie tym na laminat, który pierwotnie jest całkowicie pokryty miedzią, nakładany jest światłoczuły fotopolimer, a jego wybrane obszary zostają utwardzone za pomocą promieniowania UV w naświetlarce. Proces odbywa się w pomieszczeniach, gdzie używane są źródła światła pozbawione promieniowania UV – chroni to przed przypadkowym naświetleniem. Co więcej, dla zachowania wysokiej jakości odwzorowania mozaik, w pomieszczeniach tych musi być utrzymywany bardzo wysoki poziom czystości oraz monitorowana na bieżąco temperatura powietrza i wilgotność.
W tradycyjnej metodzie naświetlania zewnętrznych warstw miedzi używa się klisz pozytywowych, które są drukowane na tzw. fotoploterze i następnie wywoływane – mozaika jest tam odwzorowywana za pomocą jej czarnych elementów. Następnie klisze oraz pokryte fotopolimerem formaty produkcyjne trafiają do naświetlarki, która umożliwia jednoczesne naświetlanie obu stron (top i bottom). Miedź znajdująca się pod obszarami utwardzonymi zostaje natomiast usunięta podczas dalszego procesu trawienia. Obwody jednostronne oraz warstwy wewnętrzne naświetlane są z kolei kliszami negatywowymi, z uwagi na pominięcie procesu metalizacji.
Renomowani producenci PCB, w tym TS PCB, używają wysoce zaawansowanych systemów naświetlania. W celu jak najdokładniejszego geometrycznego rozmieszczenie mozaik na kliszy względem formatu produkcyjnego stosowane są specjalne systemy bazowania i naświetlania. Jednym z nich jest system OLEC – gwarantuje on automatyczne bazowanie na podstawie punktów referencyjnych umieszczonych na formacie produkcyjnym oraz kliszy (rys. 1).
Rys. 1. Naświetlarka OLEC – przygotowanie do naświetlania.
Kolejną zaletą systemu OLEC jest prostopadłe zorientowanie promieni UV względem laminatu na całej powierzchni, co zwiększa precyzję naświetlania i eliminuje problemy charakterystyczne dla starszych systemów, wynikające ze zmiennego kąta naświetlania i skutkujące podświetlaniem fotopolimeru.
Urządzenia najnowszej generacji umożliwiają bezpośrednie naświetlanie fotopolimeru z pominięciem klisz. Przykładem tego typu naświetlarek jest LEDIA - jeden z osiemnastu zbudowanych na świecie egzemplarzy tego urządzenia pracuje w TS PCB. Największą przewagą tej technologii jest plotowanie (naświetlanie) obrazów w skali zmiennej, dopasowywanej na bieżąco do rozmiaru formatu produkcyjnego – eliminuje to zjawiska odkształcenia laminatu i zapewnia idealne zgranie mozaiki z owiertem.
Warstwy opisowe oraz maska antylutownicza
Następnym etapem produkcji PCB jest nakładanie masek antylutowniczych (soldermaski) na wytrawione powierzchnie formatów produkcyjnych, a następnie warstw opisowych elementów. Są one wykonywane za pomocą specjalnej termoutwardzalnej farby światłoczułej. Soldermaski mogą być wykonywane dwoma sposobami: metodą sitodrukową oraz kurtynową (tzw. fotomaska).
Metoda sitodruku daje szerszy wachlarz wyboru typu oraz koloru farby i nie wymaga kosztownego zaplecza maszynowego. W tym przypadku soldermaska nakładana jest na cały format produkcyjny, ale poprzez specjalne sito odwzorowujące rozmieszczenie punktów lutowniczych. Metoda ta jest bardziej czasochłonna od kurtynowej i trudniej uzyskać parametry obrazu maski równoważne masce kurtynowej.
Natomiast w metodzie kurtynowej format produkcyjny przechodzi przez szeroki strumień (wodospad) farby (rys. 2) pokrywającej go w całości.
Rys. 2. Format produkcyjny (na dole) przechodzący przez kurtynę maski (górna część zdjęcia).
Wstępne utwardzenie nałożonej warstwy odbywa się w podwyższonej temperaturze, co zabezpiecza jej powierzchnię przed uszkodzeniami mechanicznymi podczas kolejnych operacji. Metoda kurtynowa jest wyjątkowo dokładna i wydajna, a także pozwala zachować wysoką czystość powierzchni laminatu. Niestety pojedyncza linia kurtynowego nakładania soldermaski może wykorzystywać tylko jeden typ farby oraz kolor maski antylutowniczej (najbardziej popularny jest zielony), a jej przezbrojenie jest bardzo kłopotliwe.
Jeśli chodzi o warstwy opisowe - występują dwie metody ich nakładania: sitodruk, gdzie farba opisowa jest nakładana selektywnie w wybranych obszarach, a następnie utwardzana; drugą metodą jest fotodruk, który polega na nakładaniu farby na cały format produkcyjny oraz wywoływaniu wybranych obszarów. Fotodruk pozwala na uzyskanie obrazu o wysokiej rozdzielczości kosztem zużycia większej ilości materiału. Metoda ta stosowana jest głównie dla projektów o mniejszych powierzchniach oraz takich, w których wymagana jest najwyższa jakość warstw opisowych.
Naświetlenie fotomaski i fotoopisu przebiega analogicznie jak w przypadku wywoływania mozaik – wykorzystywane są tutaj klisz. Wykorzystanie w tym obszarze metody naświetlania bezpośredniego stwarza trudności technicznie w realizacji, z uwagi na fakt, że konieczna jest zdecydowanie większa moc naświetlania niż dla fotopolimeru (głównie ze względu na grubość). W przypadku zastosowaniu do tego celu systemu LEDIA dostarczenie niezbędnej energii naświetlania trwałoby zbyt długo (pojedyncze minuty). Wartą uwagi alternatywą dla nanoszenia opisu metodą sitodruku może być użycie do tego celu drukarki automatycznej, która w swoim działaniu przypomina działanie tradycyjnej komputerowej drukarki atramentowej.
Obróbka mechaniczna
Rozpowszechnionym formatem plików dedykowanych do obróbki mechanicznej jest Excellon (obecnie w wersji nr 2), wykorzystywany do bezpośredniego sterowania maszynami CNC. Typowa dokumentacja produkcyjna zawiera zestaw plików dla maszyn CNC opisujących obróbkę mechaniczną projektu, najczęściej frezowania. Prawidłowy plik musi zawierać definicje średnic narzędzi, które mogą być umieszczone w jego nagłówku lub oddzielnym pliku. Warto pamiętać, że producenci PCB podane wymiary narzędzi interpretują jako docelowe średnice otworów lub wymiary szczelin, o ile nie zostało to inaczej określone w specyfikacji technologicznej. Co więcej, nagłówek pliku powinien zawierać dodatkowe informacje o użytej jednostce (mm, cale), skali oraz pominiętym układzie zer wiodących lub znaczących. Frezowanie oraz otworowanie można zapisać również w formacie Gerber, co ma swoje zalety: eliminuje problem centryczności oraz dokładności warstw mechanicznych względem pozostałych.
Warto pamiętać, że każda operacja obróbki mechanicznej może być wykonywana w inny sposób, przez co posiada indywidualne charakterystyczne ograniczenia procesowe wpływające na możliwości zastosowania w projekcie. W przypadku projektów o zróżnicowanej obróbce mechanicznej warto generować osobne pliki dla poszczególnych operacji i prawidłowo je opisać. Takie postępowanie redukuje możliwość błędnej interpretacji zamysłów projektanta.
Dokumentacja produkcyjna zawiera również dodatkowe niezbędne definicje, komendy oraz zmodyfikowane średnice narzędzi, dzięki czemu możliwe będzie osiągnięcie wskazanych w projekcie wymiarów. Jest to szczególnie istotne zwłaszcza dla otworów i szczelin metalizowanych, dla których trzeba uwzględnić dodatkową warstwę miedzi galwanicznej oraz powłoki wykańczającej (cynowanie, złocenie). Standardowo średnice narzędzi takich otworów inkrementuje się o 0,1 mm i w ostateczności uzyskuje się otwory o średnicy oczekiwanej przez projektanta, przy zachowaniu typowej tolerancji + 0,1 mm / - 0,05 mm.
Oprócz standardowych programów wiercenia i frezowania dokumentacja produkcyjna może zawierać także programy fazowania i rylcowania zawierające głębokość oraz współrzędne położenia linii rylcowania. Najczęściej zarówno frezowanie, jak i rylcowanie nie jest wskazane w projekcie bezpośrednio za pomocą dedykowanych plików, lecz w postaci warstw mechanicznych z obrysem oraz liniami rozdzielającymi poszczególne obwody np. w panelu. Czasami powoduje to niestety rozbieżności w interpretacji skutkujące pominięciem niektórych elementów obróbki podczas produkcji obwodów.
Testowanie
Dokumentacja produkcyjna zawiera również programy do testowania elektrycznego i optycznego. Producenci płytek drukowanych wysokiej jakości, w tym TS PCB, dokonują optycznej inspekcji obwodów AOI – sprawdzane są więc mozaiki po procesie trawienia. Inspekcja AOI obwodów jest testem wewnętrznym, wykonywanym niezależnie od wymagań klientów. Proces ten polega na porównaniu zeskanowanego obrazu rzeczywistego obwodu z obrazem wygenerowanym na podstawie pierwotnego projektu. Weryfikuje się różnice w obrazie obwodów wyprodukowanych oraz określa się, czy mieszczą się w dopuszczalnej tolerancji.
a) .JPG)
b) 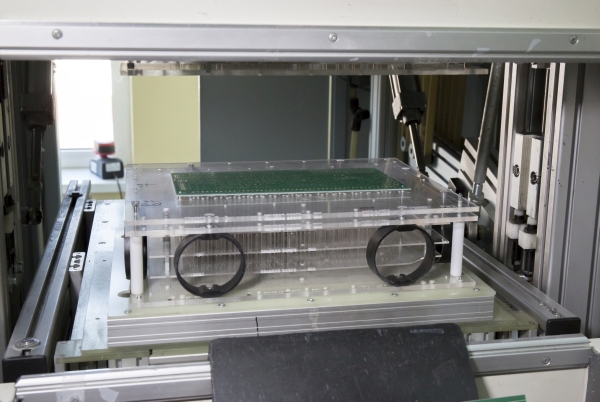
Rys. 3. Testery obwodów drukowanych: a) palcowy, b) adapterowy.
Ze względu na rosnący stopień skomplikowania PCB, poza testowaniem optycznym, konieczne jest ich testowanie elektryczne. Analogicznie jak dla AOI program do testowania elektrycznego tworzony jest na bazie pierwotnych plików projektu, niezależnie od dokumentacji przygotowywanej przez inżynierów CAM. Dzięki temu sieć połączeń wyprodukowanej płytki drukowanej porównywana jest ze wzorcem, co pozwala na wychwycenie błędów powstałych podczas produkcji.
Proces testowania elektrycznego najczęściej wykonywany jest na dwa sposoby: Bed Of Nails, określany również jako testowanie adapterowe (rys. 3b). oraz Flying Probe, nazywany niekiedy testowaniem palcowym (rys. 3a). Testery adapterowe posiadają mniejsze pole robocze niż testery palcowem oraz ograniczoną rozdzielczość rozmieszczenia igieł testujących i kołków montażowych. Wykonanie adaptera dopasowanego do konkretnego projektu jest bardzo czasochłonne. Jednak niewątpliwą zaletą tej metody jest niezwykle krótki czas testowania rzędu pojedynczych sekund na obwód lub panel. Testowanie palcowe polega natomiast na kontroli ciągłości oraz pojemności badanych sieci za pomocą ruchomych sond umożliwiających pomiary z obu stron PCB, co umożliwia testowanie najbardziej zaawansowanych obwodów HDI, także umieszczonych w formatach produkcyjnych.
Podsumowanie
W artykule został przedstawiony przebieg procesu przygotowywania dokumentacji produkcyjnej płytek drukowanych na bazie dokumentacji projektowej dostarczonej przez klienta. Prawidłowe przygotowanie dokumentacji projektu ma kluczowe znaczenie dla przebiegu procesu produkcji, a także zapewnienia jak najwyższej jakości oraz niezawodności obwodów. Należy zatem zachować szczególną uwagę podczas formułowania wymagań technologicznych, a obwody drukowane projektować zgodnie z wymaganiami producentów PCB oraz powszechnie stosowanymi standardami.