Prime factors of printed circuit board quality and durability
25.11.2015
It is difficult to imagine a modern electronic device that lacks a PCB. The continuing development of technologies and fierce market competition force electronic equipment manufacturers to improve product functionality and appeal by adopting the state of the art solutions. This usually requires packing more specialised and integrated microprocessor circuits on PCBs, which allow further downsizing of devices and reduction of production costs while improving performance and utility features.
PCBs become smaller and smaller, and more saturated with integrated circuits and electronic modules, entering the HDI class. Assured high quality and durability of HDI circuits are preconditioned by, among others, environmental factors (humidity and temperature) has been more difficult to achieve to PCB designers and PCB manufacturers. This article presents the damaging effects of corrosion in PCBs and CAF formation in dielectric materials; the factors have the defining impact on PCB quality and durability.
Humidity is the arch enemy of all electronic products. It is the prime driver of PCB corrosion, and the mechanism here is alike the corrosion mechanisms we can witness everywhere in our world. Water condensates on PCB surfaces forms electrolytic pathways for electric charges. THT lead-outs and non-solder masked mosaic components act like electrodes (pairs of anodes and cathodes) where specific electrolytic reactions occur.
Cathodes are subject to atmospheric oxygen reduction, whereas anode has metal oxidation with the metal passed to the electrolytic solution (see Fig. 1). Image 2 depicts corrosion on various PCBs. Corrosion may result in open circuits on thin paths or shorting of mosaic components (see Image 2a) by creeping metal decomposition products, which mainly include copper. The consequence is (usually) irreversible failure of the electronic circuit and its whole device.
Fig. 1. Corrosion reaction mechanism.
The corrosion rate depends, among others, on the following ambient factors: temperature, water condensate components on the PCB, and the frequency of wet/dry cycles, which is decisive to the development of creeping corrosion. Wetting a PCB with a water solution generates corrosion products which are crystallized when water evaporates in the dry cycle and become evident as specific circles (see Image 2c).
The crystalline circle radii grow with the number of the wet/dry cycles. Other PCB corrosion rate contributors include atmospheric pollutants with the growing concentration of corrosive gases, as well as the popularity of portable electronics; these devices are exceptionally exposed to varying ambient conditions.
Corrosion may also occur on PCBs that are not operated in harsh environmental conditions. Here the most often cause of corrosion are errors of PCB manufacturer's technological processes and assembly stage errors:
- Bad cleaning of PCB surfaces during the production process, and insufficient finish of PCB pads;
- Improper storage of PCBs prior to assembly and bad post-assembly PCB surface cleaning.
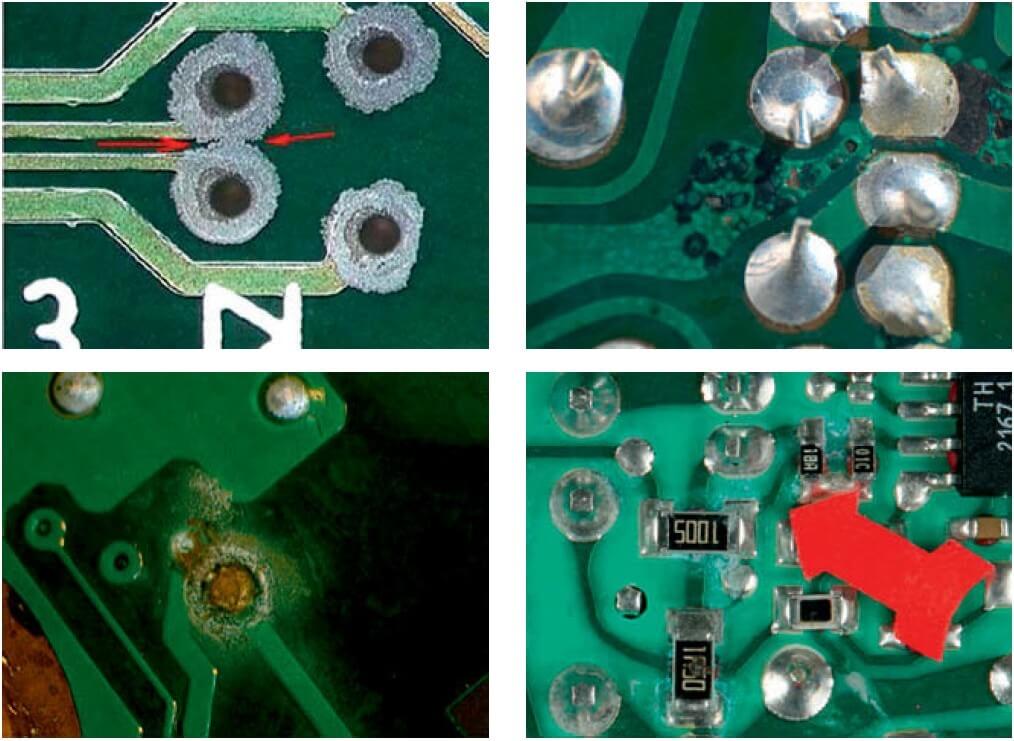
Fig. 2. Various examples of PCB corrosion.
PCBs subjected to HASL processing are especially exposed to corrosion from superficial contamination with production substances. Errors in HASL may result in deposition of a layer comprising polymerised flux components. The layer is often hardly visible and hard to remove in the PCB cleaning process.
When the affected product enters its operating stage, the contamination layer may release ions that facilitate corrosion. Corrosion may also be accelerated by incorrect PCB pad finishing. This problem is usually caused by deposition of a protective layer (e.g. resists or gold plating) that is too thin or too porous. A protective layer that is too thin or porous facilitates ingress of corrosive agents to the sensitive copper or nickel coats.
The composition of fluxing agents used in the assembly processes is adjusted to leave no deposits. However, flux decomposition products may residually survive on the PCBs, which depends on the soldering performance and the number of temperature cycles of the flux. The contaminants become ionic, which greatly accelerates the corrosion rate. Human sweat is a source of chloride ions that favour corrosion. Touching PCBs without proper gloves may also contribute to the development of corrosion centres.
The PCB corrosion risk can be well reduced by ordering the PCBs from manufacturers that offer high quality and reliable products; those suppliers certainly follow the strict principles of production purity control. A similar approach is recommended at the assembler stage. Moreover, designers who build equipment intended for extreme operating environments should consider additional protection of PCBs with special conformal coating varnishes that effectively protect against damaging humidity, extreme temperatures and other ambient conditions. Most assemblers offer protective conformal coating.
Another negative phenomenon that resembles corrosion is the development of conductive anodic filaments in the laminate dielectric material, abbreviated as CAF. CAF is an electrochemical reaction where the applied voltage results in chemical dissolution of the via conductor and in carriage of the conduction ions along the dielectric fibres (see Fig. 2).
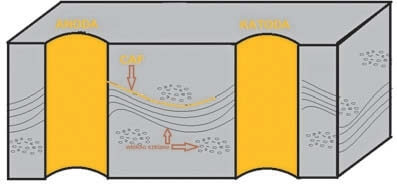
Fig. 3. Development of CAF between vias.
This forms conductive pathways which may cause current leakage or mosaic shorting. The root cause of CAF is the delamination between the base components of most laminates, i.e. resin and glass fibres. The voids created by incomplete wetting of glass fibres with resin are necessary for the metallic ion transport to occur. The second necessary condition is humidity which facilitates electrical migration of ions.
The basic method of CAF elimination is to order PCBs from manufacturers who use quality laminates from acclaimed vendors. The CAF risk in those materials is largely reduced. Not unlike with corrosion, compliance with specific processing rules during PCB manufacturing and assembly also has a major impact on CAF reduction. The particularly significant factors of PCB production include:
- The inner layer surface purity prior to pressing: event a slightest ionic contamination from incorrect flushing may contribute to the growth of conductive pathways;
- Proper prepreg flowing: incorrect storage and use of expired prepregs may deteriorate the glass fibre wetting with resin during the pressing process;
- Drilling quality: when it is insufficient, the galvanic solutions are trapped between the reinforcing fibres and provide ideal conditions for CAF;
- Strict monitoring of PCB pressing and hole desmearing: errors in the pressing process contribute to deterioration of adhesion between the layers. Improper desmearing, similar to bad drilling quality, may entrap certain components of processing baths between the glass fibres.
Proper storage of produced PCBs is crucial to PCB assembly. Wet PCBs favour delamination during the assembly process, and the defect is difficult to detect. The areas especially prone to delamination are PCB edges or millings, because their humidity absorption is increased without the solder resist.
A major impact on CAF development is caused by excessive exposure of the PCB temperature cycles during assembly. Thermal overloading may result in delamination or chemical destruction of the laminate resin, which in turn creates voids within the dielectric material. All of this also favours CAF.
Note that CAF and corrosion are driven by harsh operating conditions in the PCB environment and errors at the manufacturing and assembly stages. The risk of both effects can be minimised by preserving PCBs exposed to a harsh environment with conformal coating, and ordering PCB production and assembly from acclaimed vendors who guarantee high quality and purity of processing.